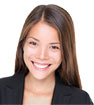
ATO Load Cells

+1 800-585-1519 (Toll-free)
Home » Wiki
The strain gauge load cell is based on the principle that the elastic element/sensitive beam is elastically deformed under the action of an external force, so that the strain gauge (conversion element) pasted on the surface thereof is also deformed along with the strain gauge. After the strain gauge is deformed, its resistance value will change (increase or decrease), and then the corresponding measurement circuit converts the resistance changes into an electric signal (voltage or current), thereby completing the process of converting external force into electric signals.
The high-temperature-resistance weighing is a specialized weighing technology widely used among metallurgy enterprises. The high-temperature-resistance steel-clad electronic scale adopted the multi-sensor modularized structure. For example, the steel-clad scale ranging from 1t to 300t adopts four 150t sensors, and the steel-clad scale ranging from 1t to 150t adopts four sensors. Products of the kind are characterized by high-temperature-resistance (the system could work steadily for a long time when the temperature is ≥250℃) and high-resistance (300% shock resistance).
Reasonable applications of the multi-sensor technology can create favorable working conditions for electronic weighing instruments, change the input and output characteristics, reduce the electronic weighing instruments' energy consumption, and improve the system's anti-interference ability. Therefore, to study the multi-sensor technology is of vital practical signifance.
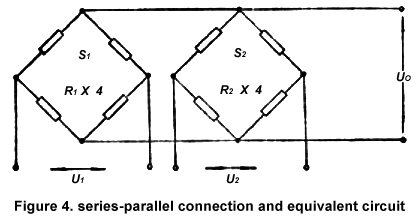
Reasonable applications of the multi-sensor technology can create favorable working conditions for electronic weighing instruments, change the input and output characteristics, reduce the electronic weighing instruments' energy consumption, and improve the system's anti-interference ability. Therefore, to study the multi-sensor technology is of vital practical signifance.
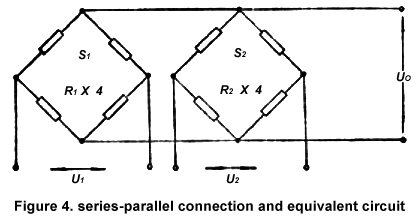
The medium-sized and large electronic scales are made up of several strain gauge load cells (hereinafter abbreviated as the 'load cell'). There is only one meter for weight display. Several load cell group scales are connected through two means, either group-scale in series or group-scale in parallel. Due to rapid development of electronic technologies and popularization of SCM, weighing instruments have experienced a significant improvement of output sensitivity, which can fully satisfy the technological requirements of the group-scale in parallel. Therefore, the group-scale in series has been eliminated, and the group-scale in parallel is more widely adopted.
However, affected by civil construction and mechanical installation, the electronic weighing instrument can easily cause uniform distribution of force on various load cells. Besides, because of manufacturing differences of load cells, various parameters cannot ensure their consistency despite of circuit compensation and adjustment. As a result, unacceptable eccentric error is caused for the electronic balancing instrument with multi load cells working in parallel connection. Whether the eccentric load test is qualified or not in the electronic weighing instrument industry is a key item for whether the electronic weighing instrument can pass the test and be used normally. Therefore, it is necessary to explore an effective and reasonable debugging method to reduce the eccentric error by analyzing the eccentric load debugging principle of load cell parallel group-scale.
However, affected by civil construction and mechanical installation, the electronic weighing instrument can easily cause uniform distribution of force on various load cells. Besides, because of manufacturing differences of load cells, various parameters cannot ensure their consistency despite of circuit compensation and adjustment. As a result, unacceptable eccentric error is caused for the electronic balancing instrument with multi load cells working in parallel connection. Whether the eccentric load test is qualified or not in the electronic weighing instrument industry is a key item for whether the electronic weighing instrument can pass the test and be used normally. Therefore, it is necessary to explore an effective and reasonable debugging method to reduce the eccentric error by analyzing the eccentric load debugging principle of load cell parallel group-scale.
As known to all, shear stress cannot be measured, but it can generate the principal strain with both stretching and compression load, and constituting an angle of 45°with the shear elastic elements' central axis. This is what is required by Wheatstone bridge made up of the load cell. Since the shear stress elastic elements uniformly distributed along the strain stress central axis along the shear strain, changes of the loading points will not influence the output sensitivity. The double-shear resistance strain gauge is pasted on the abdomen plate of the I-shaped cross-section, which is not sensitive to eccentric, lateral and torsional load. At the same time, the sensitivity symmetry is high when receiving stretching load and compression load at the same time. The shear beam-type elastic elements have a small height and the assembled electronic scale has a low gravitational center, which fully overcomes the inherent defects of normal strain elastic elements with the cylindric, columnar and cantilever structure. Every year, shear stress elastic elements with different structures are developed and applied to different electronic weighing instruments, thus ushering a new trend for development of the strain load cell.
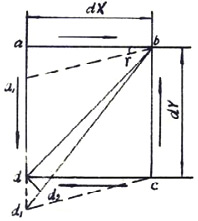
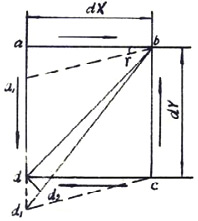
The elastic element of column type load cell is normal stress cylindrical and columnar elastic elements. The normal stress cylindrical and columnar elastic elements can be divided into the single-column type, single-cylinder type and multicolumn type. The single-column type features the cylindric, columnar, truncated columnar, and truncated cylindric structure. Upon customer requires, other structures, including square column, square drum, prism, and edge drum, can also be adopted. Structures, including multi-cylindrical, multi-drum, and three-square-column, four-square-column, three-square-drum and four-square-drum, dominate.
Within the strain area of ideal normal stress and shearing stress elements, the strain degree should form a strict linear relationship with the externally-imposed load, which is also at the core of designing all load cell elastic elements. Difficulties to finish this process are mainly caused by limitations of structural design, computing and economic budget. Only when the load cell R&D and production rules and elastic element structural design and boundary selection principles are adhered to can the above limitations be resolved and the comprehensive influence of various factors be overcome to turn out the load cell with the minimum fluctuation.
Strain gauge load cell is made up of elastic elements (external load elastomer), strain resistance transformer elements (resistance strain gauge of different types) and inverters (Wheatstone bridge circuits). Among them, advancement and reasonability of elastic elements is the linchpin to high accuracy and stability of strain gauge load cells.
A load cell is a conversion device used to convert a weight/mass signal or a force signal into an electrical signal. The strain gauge load cell is based on the strain effect. Under the action of external force, the resistance strain gauge pasted to the surface of the elastomer is deformed together with the elastomer. After the strain gauge is deformed, the resistance value changes, and the measuring circuit will convert the changes into an electrical signal and output, which indirectly measures the external force. It can be seen that the strain gauge load cell is mainly composed of three parts, namely an elastomer, a resistance strain gauge and a measuring circuit.
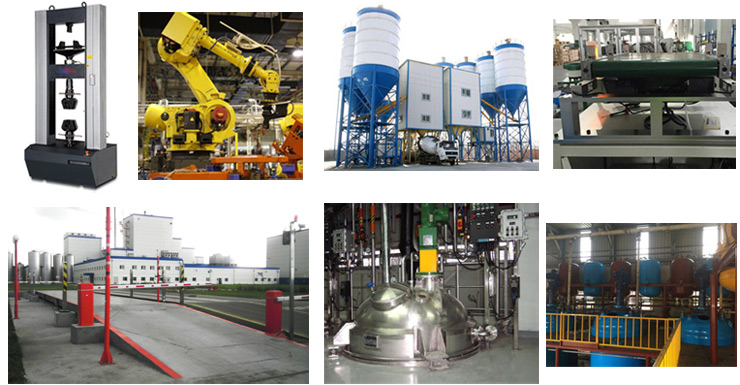
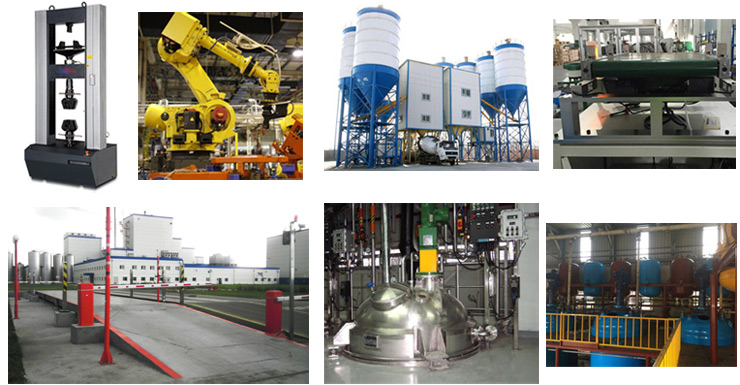
A load cell is actually a device that converts a mass signal into a measurable electrical signal. The working principle is to convert the weight of the object added to the scale pan into an electrical signal proportional to the weight, amplify and A/D convert the output electrical signal, and then to display the weighing information by other relevant circuit.