Load Cell Troubleshooting
Faults of strain gauge load cells in use often cause weighing system drift, unstable display or non-display of data. Next this article mainly introduces some common faults, troubleshooting methods and steps of analog load cells.
There are many causes for load cell faults, but in summary, they can be divided into internal and external causes. The internal causes mainly refer to the faults caused by the load cell itself, while the external causes refer to the damage caused by human or natural factors, such as load cell overload, impact, or accidental fall, forceful drag of load cell cables, thunder strike or large current passing through the load cell, chemical corrosion, dampness, high dust environment, or the aging of components in load cells and so on. For these fault causes, we can analyze them from several main parts of the load cell. The load cell consists of three parts: elastic element, resistance strain gauge and output circuit. From the perspective of load cell faults, the essence is output fault. Therefore, we should use the correlation method to analyze, namely analyzing with the signal output process of the load cell itself.
To solve problems more conveniently, we can refer to the signal processing principles in DSP and transfer the four steps into four modules, each of which shall be responsible for its functions. All these modules deal with transformations in assembly line form.
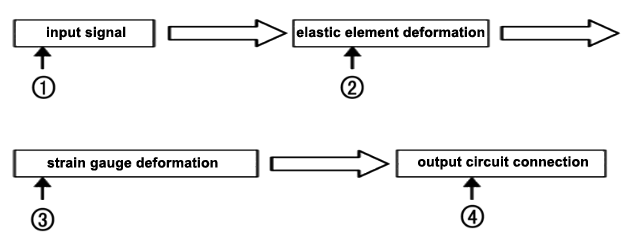
Based on the correlation method, output fault may occur in each module before final output. In the process of elastic element deformation to strain gauge deformation, it contains the mechanical to electronic conversion, during which glue plays a key role of an intermediary media. Therefore, we can precede exclusive method for such failures with the modular step-by-step.
Fault 1: When the load is added to the load cell, there is no weight display on the load cell controller.
There are many causes for load cell faults, but in summary, they can be divided into internal and external causes. The internal causes mainly refer to the faults caused by the load cell itself, while the external causes refer to the damage caused by human or natural factors, such as load cell overload, impact, or accidental fall, forceful drag of load cell cables, thunder strike or large current passing through the load cell, chemical corrosion, dampness, high dust environment, or the aging of components in load cells and so on. For these fault causes, we can analyze them from several main parts of the load cell. The load cell consists of three parts: elastic element, resistance strain gauge and output circuit. From the perspective of load cell faults, the essence is output fault. Therefore, we should use the correlation method to analyze, namely analyzing with the signal output process of the load cell itself.
To solve problems more conveniently, we can refer to the signal processing principles in DSP and transfer the four steps into four modules, each of which shall be responsible for its functions. All these modules deal with transformations in assembly line form.
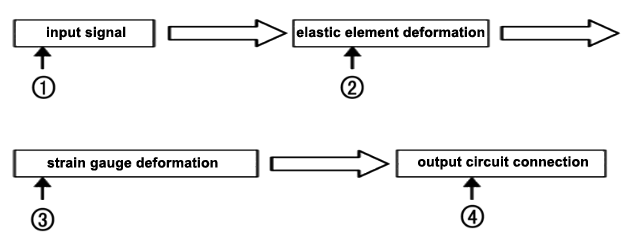
Based on the correlation method, output fault may occur in each module before final output. In the process of elastic element deformation to strain gauge deformation, it contains the mechanical to electronic conversion, during which glue plays a key role of an intermediary media. Therefore, we can precede exclusive method for such failures with the modular step-by-step.
- Faults of input signal are very clear, and weight change can be clearly seen.
- Faults of elastic element deformation are mainly reflected in elastic element design and material, which can be verified by testing the repeatability, nonlinearity and hysteresis of load cell.
- Faults of strain gauge deformation are mainly reflected in the resistance value change of input and output resistors, which can be judged by testing the input and output resistance values. During the testing, the load cell should be disconnected from junction box and other testing equipment. Measure the input and output resistance value in order, and then compare if the testing values are consistent with the values on product certificate.
-
Faults of output circuit connection are mainly reflected as no voltage or current at the output end, which can be judged by measuring if there's output signal at the cable end.
Fault 1: When the load is added to the load cell, there is no weight display on the load cell controller.
- Firstly, check whether the output circuit is normally connected, measure whether the input and voltage output of the bridge circuit are normal. If there is a fault in the voltage circuit, remove it and make further check.
- After checking the connection of output circuit, check the connection between strain gauge deformation and output circuit connection, check whether there is virtual welding or open welding at the bridge welding joint that makes the bridge not to work.
- If there's no connection fault between the output circuit connection and the resistance strain gauge deformation, check the resistance strain gauge deformation, check whether there are foreign bodies in the load cell, whether the strain gauge has strain, whether the resistance has changed.
-
Problem occurs in elastic element deformation, the deformation of strain gauge doesn't meet the requirements.
- There's virtual welding at of the connection between the output circuit and one bridge arm of bridge circuit.
- Strain gauge deforms, or the glue separates at the place where the strain gauge is pasted.
- Value of insulation resistance between bridge and elastic bottom decreases at the joint of strain gauge deformation and elastic element deformation.
-
Problems occur at the deformation of elastic element, strain gauge deformation doesn't meet the requirements.
- Problems occur at the deformation of elastic element, the faults may be caused by elastic element falling, collision, partial fracture or over-fatigue, which make the elastic element to lose proper stress variation and consequently can't read accurately.
- Problems occur at the deformation of resistance strain gauge. A certain reason leads to supply bridge voltage rise or overheat of the strain gauge, thus damaging the adhesive glue of strain gauge and changing the resistance.
-
Problems occur at the output circuit connection. Used in high temperature or in environments with large temperature change, output circuit components are unstable or damaged.
- Problems occur at the deformation of elastic element, the elastic element changes unstably.
- Problems occur at the deformation of resistance strain gauge, its properties are not that good.
- Problems occur at the connection between the elastic element deformation and the resistance strain gauge deformation, the adhesive agent goes bad and makes the strain gauge not firmly.
-
Problems occur at the output circuit connected bridge circuit, the components performance is not stable or external affects the circuit board output.
- Problems occur at the deformation of elastic element, the elastic element changes unstably.
- Problems occur at the elastic element deformation and the strain gauge elastic element, the glue is not properly selected or goes bad due to aging, or fails in humid environment.